Refrigeration Air Cooled Condenser for cold room have several models. One type is like a panel, we call it FNH type condenser, this type is very popular, but if the condensing unit is too large, this type can not work well. So engineer designed and engineered another type, a first fin group and a second fin group are installed in the casing, and the two fin groups are installed in the casing in a “V” shape. We call it FNV type. In addition, for box unit, we also have U type and L type. Please check following pictures, you will have clear idea about these types.
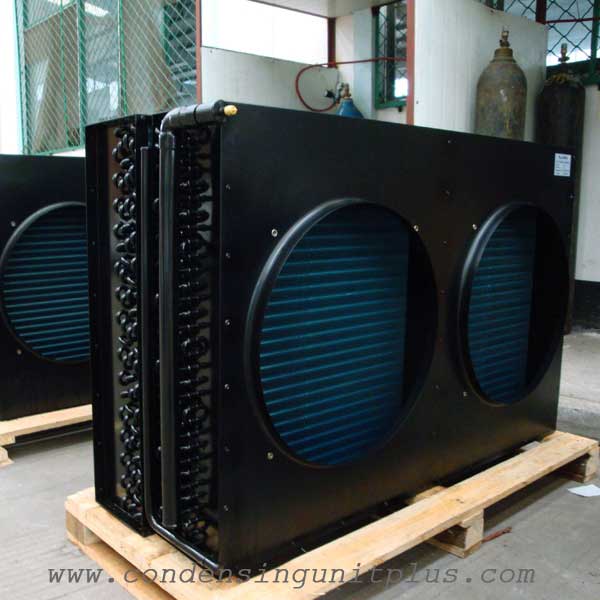
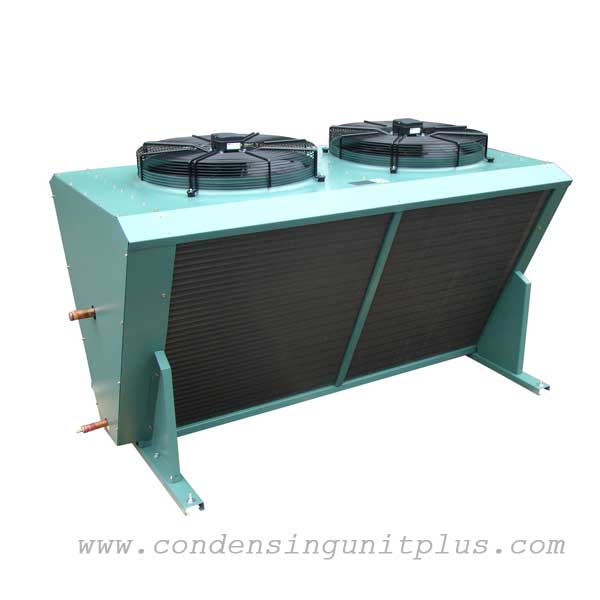
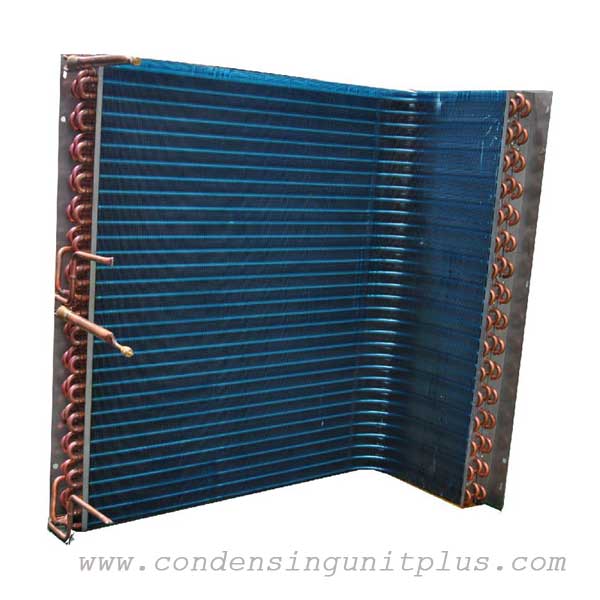

The function of the air cooled condenser is heat exchange. Simply put, the heat absorbed in the room is discharged to the outside through the air cooled condenser. The specific principle is the high-temperature, high-pressure gas refrigerant discharged from the compressor, and the heat of the refrigerant in the condenser is taken away by the axial fan of the outdoor unit. Except air cooled, cold room condenser also have water cooled, evaporated cooled etc. Refrigeration air cooled condenser is more popular for cold room. Because its work does not need water and is easy to install. The condensing unit with air cooled condenser is often used for areas where the water source is tight in the region. The longer the annual operating hours, the more advantageous the air-cooled refrigeration unit is; the annual comprehensive cost of the air – cooled refrigeration unit is lower than that of the water cooled system.
Refrigeration air cooled condenser for cold room include two main parts, the aluminum fin and copper pipe. Following are some main production process of this two parts for your reference.
The aluminum foil is punched with a high speed punch. The high pressure press is a device for punching air conditioner heat exchanger fins. The operator installs the aluminum foil on the uncoiler, sets the fin parameters, installs the material in the manual, single – cycle operation state, and then runs continuously in the continuous running state to continuously produce and stack the fins. The raw material used for processing the fins is aluminum foil, and the auxiliary material is mainly fin processing oil.
The whole high flushing equipment mainly includes unwinding machine, quantitative oil feeder, fin mold, punching machine, bed body, fin vacuum adsorption device, collecting device, waste collecting device and so on.
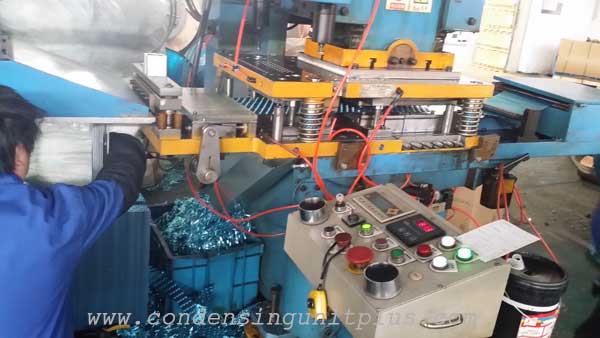
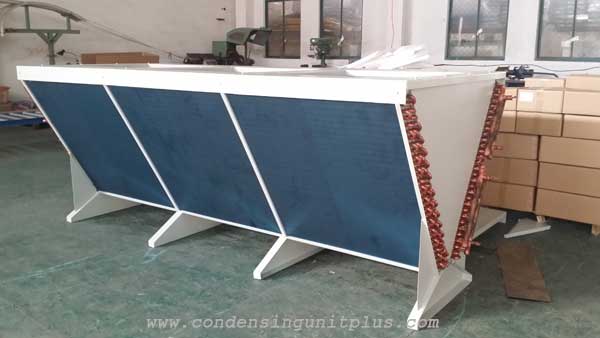
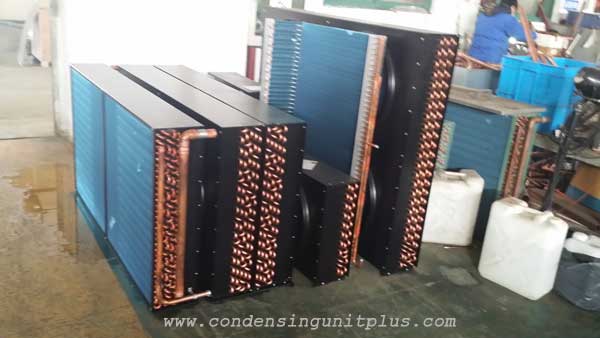
Tube expansion control points:
- The use of non shrinking equipment to expand the mouth, the quality of the bell mouth has been significantly improved. Since the non-shrinking technology adopts the form of clamping at both ends of the jaws, the size of the two ends B can be ensured, and at the same time, the end of the straight tube is unloaded and the non-shrinking automatic horn action is performed to ensure the quality of the bell mouth.
- The bell mouth does not have defects such as curling, cracking and the like.
- The diagonal deviation is small, the film spacing is uniform, the lamination and the inner leakage are reduced, the expansion tube is consistent, the nozzle is consistent, and the deformation is reduced.
Welding, water inspection, pressure holding process process requirements:
- The copper tube is welded with silver-containing electrode, and the solder joint is more firm.
- Pool leak detection to ensure good product sealing.
- 6Mpa pressure test to check if the welding condition is good.
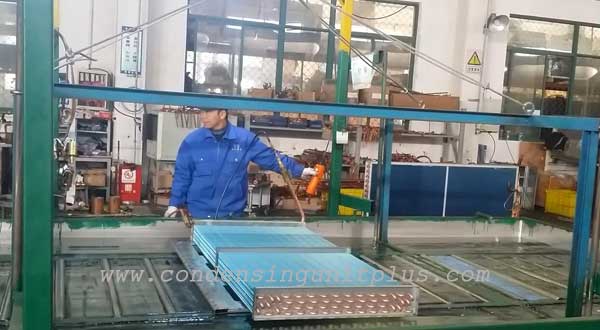
OnlyKem refrigeration air cooled condenser for cold room has exported to a lot of countries. After check our quality, some client asked OEM, some client is promoting OnlyKem brand directly. We believe that we have a booming future.